
Often times this is being started while the job is still in the quotation stages. “With IronCAD, we can quickly start to build fixtures around the part models being supplied from our customers. More often than not, this leads to some very innovative fixturing and machining methods. “At Aero-safe, we have found a niche manufacturing the difficult and nearly-impossible-to-make precision parts. “IronCAD also allows us to participate with our customers earlier on in the design process by suggesting ways that part models can be modified to allow for improved manufacturing methods. Our customers have a high level of confidence that we are manufacturing precision parts to the as-designed specification. We no longer waste time massaging data so that we can manufacture a component. “Since implementing IronCAD, we have found the flow of engineering data between ourselves and our customers to be nearly seamless. This feature, combined with the extensive list of import/export formats, which IronCAD supports, is truly amazing. To our surprise and delight, IronCAD has the capability of working in either the ACIS or Parasolid kernel - or both at the same time. It was quite astounding how IronCAD fit in so perfectly with all the needs that we had identified. “After an exhaustive search, one CAD system stood high above the rest: IronCAD. The traditional design-drawing-manufacture process is rapidly being replaced by the design straight-to-manufacture process. This wave of design data eventually makes its way to the manufacturer, who is expected to use the data as presented. Our customers have embraced the solid modeling design approach in a big way. “We also had to consider the integration of the CAD system with a new CAM system. It had to be compatible with as many CAD systems as possible while having good modeling capabilities as well as being easy to learn and use. “When Aero-safe set out to find a new CAD tool we had some very distinct and seemingly antagonistic requirements. For a small company to be able to accommodate each of its customers, maintaining licenses with all those different CAD systems would create an impossible situation.Īero-safe Technologies Inc., a supplier of precision parts and assemblies to the aerospace, satellite communications, life support, surveillance, defense, optical, and medical industries since 1981, was facing just this situation when they began a search for a CAD system that help them handle the increasingly diverse and challenging demands of their customers.Īs Rick Dorrington, CAD/CAM Manager at Aero-safe Technologies Inc., put it:
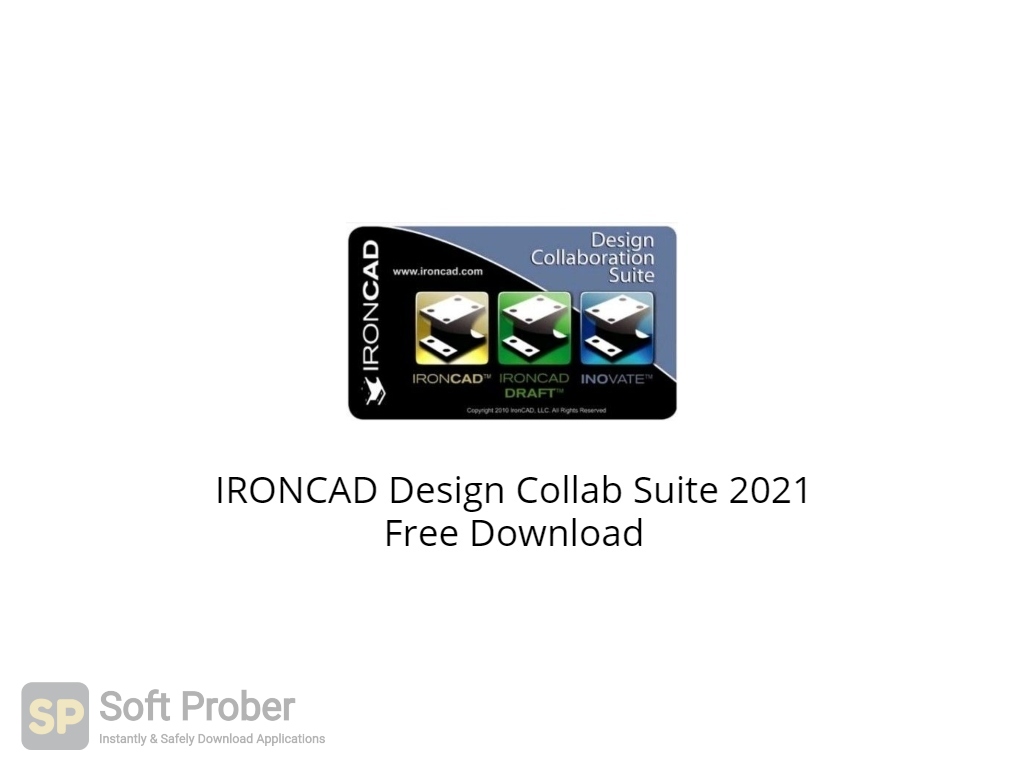
Customers are demanding ever-shorter lead times while expecting very high-quality precision parts at an aggressive price point - but they all use a different CAD system. The challenges facing small precision parts manufacturers in today’s competitive environment are extreme.
